was ist ein Andon-Cord ?
Jede Arbeitsstation in einem Prozess verfügt über einen bestimmten Pullcord oder Zugschnur (typischerweise ein buntes Kabel, das in Reichweite hängt).
Wenn ein Arbeiter ein Problem erkennt, zieht er an der Andon-Cord und stoppt die Produktion an seiner Station sofort.
So einfach ist das.
Aber dieses System ist mehr als nur eine Schnur.
Inhaltsverzeichnis
ToggleAndon was bedeutet das?
Ursprünglich in der Produktion von Toyota entwickelt, ist ein wichtiges Werkzeug für das Projektmanagement. Indem Störungen zeitnah erfasst und korrigiert werden, wird die Effizienz und Qualität der Projektleistung verbessert. Es ist ein Aspekt der Lean Manufacturing und Kaizen.
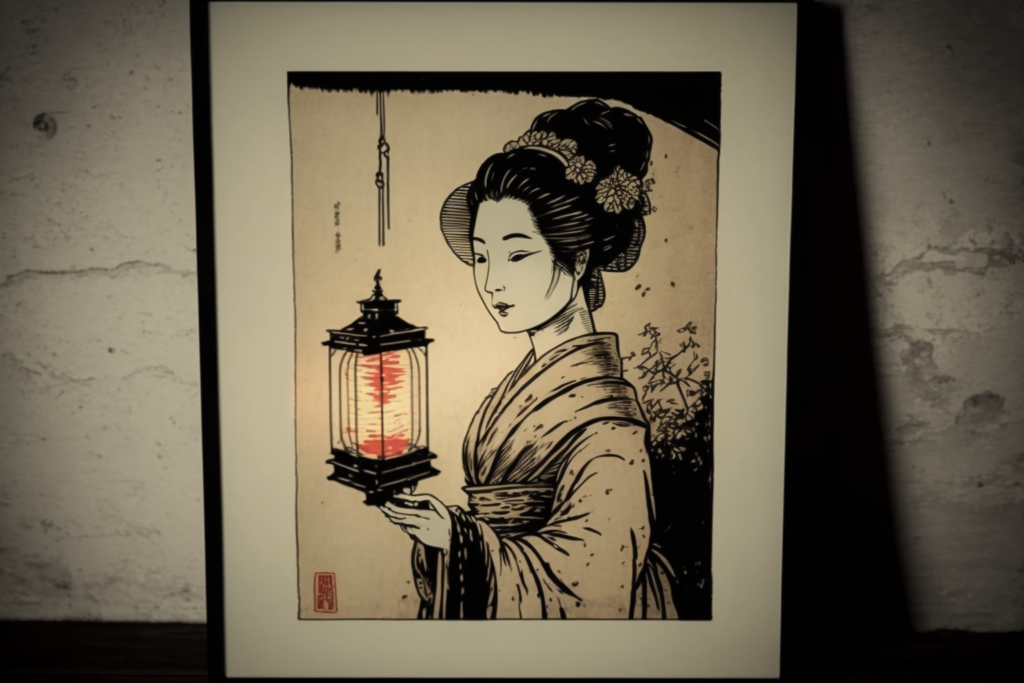
Auf Japanisch bedeutet „Andon“ (行灯,あんどん) „Laterne“ oder „Licht“.
Andon bezieht sich im wahrsten Sinne des Wortes auf eine feste, in Papier eingeschlossene Laterne; Auf einen Holz- oder Metallrahmen geklebtes Papier, in dem sich eine (Öl-)Lampe befindet.
Allerdings ich weiß, was Sie sich fragen; „Was hat ein Licht mit effizientem Fehlererkennung im Projelktmanagement zu tun?“ Machen Sie sich darüber keine Sorgen. Der lustige Name ist irrelevant, aber die darin enthaltenen Konzepte sind wertvoll.
Toyota Production System (TPS) Konzentriert sich auf die beschleunigte Berichterstattung und Lösung von Problemen, die in der Produktionslinie auftreten.
Wie funktioniert Andon genau? Hier ist, wie:
Andon reduziert die Zeit für die Datenübertragung, wenn Verzögerungen und Unterbrechungen im Produktionsprozess auftreten. Im System sind Eingabemechanismen und Ausgabemechanismen vorhanden.Einerseits, scheint es einfach. Auf der anderen Seite werden hauptsächlich manuell eingegebene Daten zu Problemen erfasst. Eines der bekanntesten Bestandteile des Systems ist das Andon-Seil.
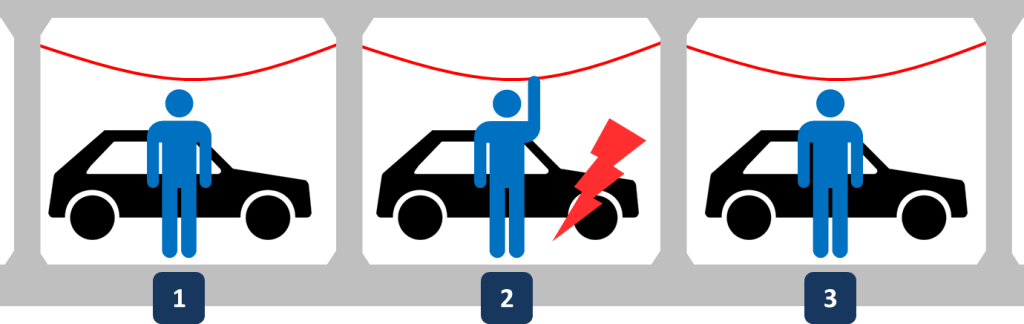
- Zugschnurstation: Jeder Arbeitsplatz ist mit einer eigenen Andon-Chord ausgestattet (normalerweise eine bunte Schnur, die in Reichweite hängt).
- Problemerkennung: Nehmen wir an, einer unserer fleißigen Mitarbeiter entdeckt ein Problem. Was machen Sie? Nun, sie machen weiter und ziehen an der Schnur. Dadurch wird die gesamte Produktion an ihrer Station sofort gestoppt.
- Signal und Alarm: Durch Ziehen an dieser Schnur hat unser Mitarbeiter das Licht aktiviert (normalerweise ein rotes oder blinkendes Licht an der Station). Daher das Wort Andon japanisches Licht. Wir nutzen dieses Licht als visuellen Hinweis für unsere Teamleiter und Vorgesetzten, dass etwas nicht stimmt.
- Schnelle Hilfe: Sobald der Teamleiter oder Vorgesetzte das Andon-Signal sieht, eilt er zur Station, um das Problem zu klären.
- Problem-solving: Jetzt kann das Team gemeinsam mit dem Mitarbeiter damit beginnen, das Problem zu diagnostizieren, die Grundursache zu identifizieren und die beste Lösung zur Behebung umzusetzen.
- Produktionsneustart: Sobald das Problem behoben, überprüft und erfasst ist, können wir die Produktion am Bahnhof wieder aufnehmen.
Visuelle Signalisierung

![[[File:Andon-Board in einem Produktionswerk.png|thumb|Andon-Board in einem Produktionswerk|alt=Andon-Board in einem Produktionswerk]]](https://upload.wikimedia.org/wikipedia/commons/thumb/4/4c/Andon-Board_in_einem_Produktionswerk.png/1024px-Andon-Board_in_einem_Produktionswerk.png)
Vorteile von Andon Prinzip
Die Verwendung in der Produktion kann nicht nur die Produktivität erhöhen, sondern auch die Mitarbeiterzufriedenheit und -motivation steigern. Durch die Verwendung von Anwendungen für das System können sie unerwartete Ereignisse schnell bewältigen, was zu einer gesteigerten Produktion und letztendlich zu verbesserten Geschäftsergebnissen führt.

1.Steigerung der Mitarbeitermotivation
Durch die Anzeige des Produktionsstatus und der Kennzahlen auf den Andon-Boards kann die Leistung der Mitarbeiter verbessert und ihr Engagement gesteigert werden. Die Steigerung der Motivation der Mitarbeiter und die Förderung eines gesunden Wettbewerbsgeistes helfen.
2. Optimierung von Produktionsprozessen
Das Andon-System erkennt Optimierungsmöglichkeiten in Echtzeit. Um sicherzustellen, dass auf unerwartete Ereignisse schnell reagiert werden kann, können wir Prozessschritte und Entscheidungen im Materialmanagement neu planen. Es ist möglich, den Betriebszustand zu überwachen und anzuzeigen
3. Erhöhte Sensibilität für Probleme und Störungen:
Erhöhte Sensibilität für Probleme und Störungen: Durch die Verwendung von Andon-Boards und Kabeln ist es einfach, Produktionsprobleme und -störungen zu erkennen, sodass alle Mitarbeiter sie sehen können. Es ist möglich, Probleme schnell zu lösen und eine effektive Zusammenarbeit zu fördern.
4. Verbesserung der Transparenz und klaren Kommunikation:
Das Andon-System trägt zur Verbesserung der Transparenz in der Fertigungsumgebung bei und fördert eine klare Kommunikation zwischen verschiedenen Abteilungen und Mitarbeitern. Die Informationen werden klar und gut sichtbar dargestellt.
In Zusammenfassung trägt das System zur Steigerung der Mitarbeitermotivation, Verbesserung der Produktivitätseffizienz, Schaffung des Problembewusstseins und Optimierung der Kommunikation bei. Es ist das Ziel, die Produktionsprozesse zu verbessern und die Mitarbeiterbindung zu fördern.
5 Branchen, die Andon-Systeme anwenden
Sie wurden entwickelt, um den Betriebszustand von Produktionslinien oder einzelnen Maschinen in einer klaren visuellen Darstellung anzuzeigen.
- Automobilindustrie
- Elektronikindustrie
- Lebensmittelindustrie
- Logistikbranche
- Maschinenbau
Visual Management ist ein Super Power
Die Effizienz steht im Mittelpunkt. Es ist wichtig, jede Minute zu nutzen und Produktionsstörungen nicht zu ignorieren. Das Ziel der Konzeption des visuellen Managements ist es, Informationen so darzustellen, dass sie auf einen Blick sichtbar und verständlich sind. Darüber hinaus, statt wichtige Daten in komplizierten Berichten oder Tabellen zu verbergen, werden sie im visuellen Management hervorgehoben und Grafiken, Diagramme und andere visuelle Hilfsmittel genutzt, um Kennzahlen und Trends darzustellen.
Tatsächlich erweitert die Echtzeitübermittlung von Fehlermeldungen die Funktion des visuellen Managements und ermöglicht eine sofortige Reaktion auf Produktionsstörungen.
Stack-Lights oder Ampelleuchten sind visuelle Hilfsmittel, die an Maschinen installiert sind und den Status jeder einzelnen Arbeitsstation in der Fertigungshalle anzeigen.
Ja, bei Stack-Lights oder Ampelleuchten gibt es eine spezifische Reihenfolge und Bedeutung der Farben. Üblicherweise folgen sie dem Ampel-Schema, bei dem Rot einen Stopp oder eine Störung signalisiert, Gelb darauf hinweist, dass Aufmerksamkeit erforderlich ist, und Grün den normalen Betriebszustand oder eine gute Funktion anzeigt. Diese Farben dienen dazu, den Mitarbeitern auf den ersten Blick den Status jeder einzelnen Arbeitsstation in der Fertigungshalle zu vermitteln.
Die Andon-Boards eröffnen zahlreiche Optionen zur Anzeige des Produktionsstatus und relevanter Kennzahlen. Es werden durchschnittliche Bearbeitungszeiten, Qualitätsspezifikationen wie FPY oder CPK, Störungen an Arbeitsstationen, Materialbedarf und weitere logistikrelevante Informationen vorgestellt. Diese Darstellungen werden auf verschiedenen Anzeigegeräten wie Großanzeigen, Stack-Lights, Touch-Terminals oder Bildschirmen angezeigt. Die Informationen können durch visuelle Hilfsmittel wie Ampelleuchten oder Farbcodes auf den Andon-Boards ergänzt werden.
Andon-Boards können visuell durch verschiedene Ergänzungen erweitert werden. Zum Visualisieren des Zustands von Produktionslinien oder Maschinen können Ampel- oder Signalleuchten verwendet werden. Andon-Boards können auch große Bildschirme oder Beamer verwenden, um Informationen wie den Produktionsstatus und relevante Kennzahlen anzuzeigen. Außerdem kann der Zustand einzelner Arbeitsstationen in der Fertigungshalle mithilfe von Stapelleuchten oder Ampeln angezeigt werden. Mithilfe dieser visuellen Ergänzungen können Mitarbeiter sofort Informationen zum Produktionsprozess erhalten und entsprechend handeln.
Die Reaktionsfähigkeit und Transparenz werden verbessert, indem Andon-Boards und Andon-Cords den Produktionsstatus und relevante Kennzahlen anzeigen. Mitarbeitern wird ermöglicht, aktiv auf Störungen, Materialmangel oder andere Fragen im Produktionsprozess mit Andon-Cords zu reagieren.
Die Mitarbeiter können aktiv auf Störungen oder Materialbedarf während der Produktion reagieren, indem sie das Andon-System und die Andon-Cords nutzen. Es wird empfohlen, Andon-Systeme zu implementieren, um die Motivation der Mitarbeiter und die Effizienz in der Produktion zu steigern.